CS & Quality Management
- Strategy (Stance, Approach, and Awareness of Risk)
- Governance
- Risk Management
- Indicators and Targets
- Major Initiatives
- Performance Data
(Stance, Approach, and Awareness of Risk)
Basic Concept
Since 1999, SEKISUI CHEMICAL Group has placed the utmost emphasis on satisfying its customers and has accordingly
practiced customer satisfaction (CS) management. Recognizing that customer satisfaction and quality are inseparable,
we have engaged in CS & Quality management since 2004 to consistently deliver sufficient value that ensures
we remain the preferred choice of customers.
In all of our business activities, we are thoroughly committed to service quality innovation and strive to constantly deliver value (products and services) that meet customers’ expectations. Based on the slogan "our quality is based on the voice of our Customers” the Group is united in its efforts to refine the competence of its employees as well as the quality of its systems, products, and services with the aim of continuously meeting the quality expectations of its customers. Our goal is to ensure that our customers choose the Group while continuing to develop and grow together over the long term.
Recognizing that the quality that makes this possible is supported by the production frontline, we emphasize strengthening fundamental quality and adhering to quality compliance.
- 15-01
SEKISUI CHEMICAL Group’s CS & Quality Management Circulation Diagram
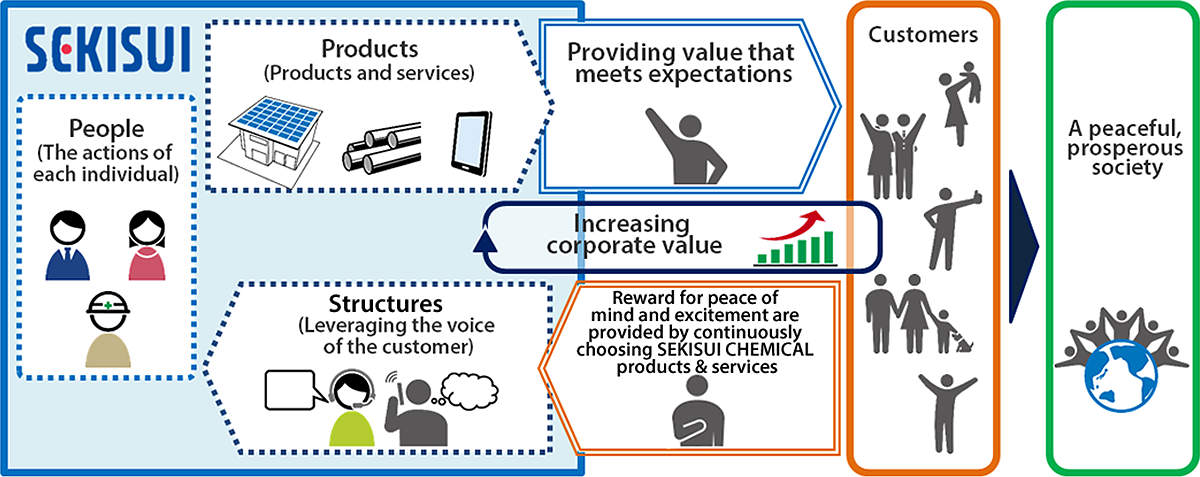
- For details, seeSEKISUI CHEMICAL Group CS & Quality Management Policy.
CS & Quality Current Medium-term Plan
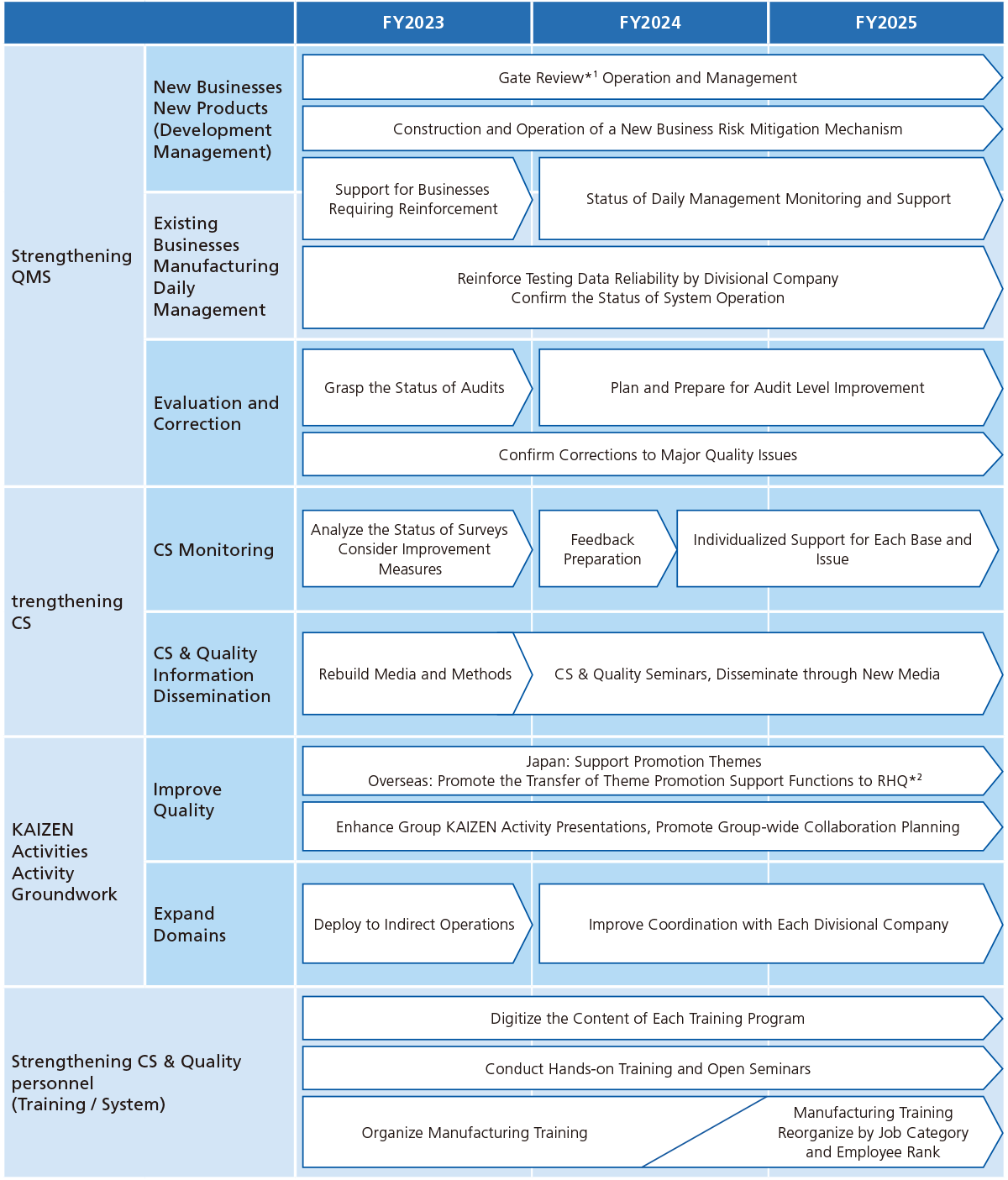
- Gate Review (GR): Systematic activities (checkpoint control function) to determine whether or not to move on to the next stage.
- RHQ(Regional Headquarters)
Awareness of Risk
Prevention of Defects, Strengthening of Daily Management, and the Elimination of Quality Data Falsification
SEKISUI CHEMICAL Group adheres strictly to quality compliance. We are working to build a culture that prioritizes quality and the prevention of fraud by continuously strengthening the foundations that support quality through such efforts as preventing defects and strengthening daily management. Especially with regard to quality data falsification, we have been working since 2020 to revise organizational systems, digitalize quality data and promote data reliability, conduct quality compliance education, and reinforce the review of new businesses opportunities in order to eradicate the root causes of risk, based on the hypothesis that quality data falsification can arise due to the insufficient allocation of resources to such areas as quality and organizational systems as well as various types pf both internal and external pressure.
Formulating Quality Guidelines
SEKISUI CHEMICAL Group engages in consistent quality control across the entire value chain, from product development to design, production, sales, and after-sales service. In order to improve the quality of its quality control in each process, we have established and published the following three guidelines.
- Development Guidelines for Strengthening Quality Assurance
The purpose is to prevent quality-related problems from occurring by predicting quality risks that may occur after commercialization. - "The Guidelines for Daily Management Activities"
A summary of the basic guidelines for day-to-day management to be implemented by the manufacturing department. - Contract / Specification Guidelines
The purpose is to reduce the risk of expanded compensation* related to product sales.
- Expanded compensation: Customer compensation in the case of product defects that extend beyond returns and exchanges to indemnify the customer for any products, workmanship, or objects that the customer has processed, installed, or used, as well as for any related damages.
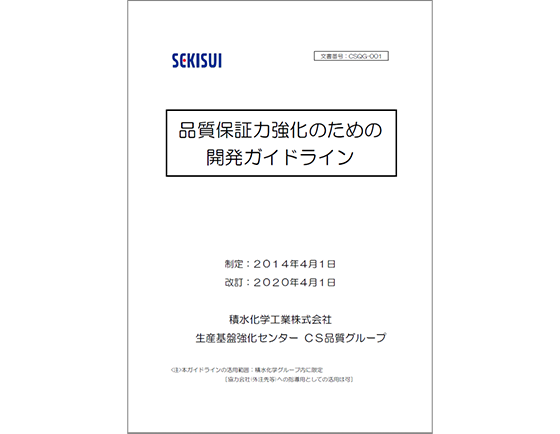
Self-declaration for Consumer-oriented Management Follow-up Activities
In January 2017, we endorsed the Consumer Affairs Agency's initiative to realize "consumer-oriented management" and implemented the “Self-declaration for Consumer-oriented Management*,” which expresses our stance and policy on the initiative.
- An activity in which a company declares that it will voluntarily engage in consumer-oriented management, takes measures based on the declaration, follows up, and discloses details of results.
- 15-05
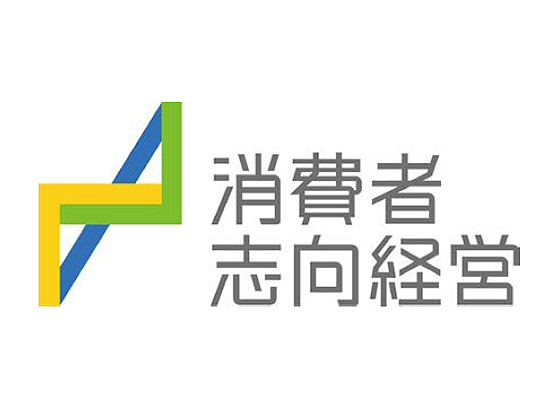
In fiscal 2023, we worked on the following initiatives based on the“ Self-declaration for Consumer-oriented Management.”
- 1.Ensuring Basic Qualities
We have established a quality assurance system covering the entire process from product development to design,
production, and sales while promoting design and development management, as well as daily management activities.
In addition, Group companies in Japan and overseas are developing and promoting Group KAIZEN Activities, in which employees in each workplace form small groups to address various topics such as improvements in quality and productivity. - 2.Creating Value That Exceeds Customers’ Expectations
We held three CS & Quality seminars to introduce internal experts and case studies to provide hints on how to create value that exceeds customers' expectations. - 3.Upgrading Technological Capabilities
In the development of new products, we held one development prevention seminar with the purpose of imparting knowledge on effective and efficient methods to prevent quality problems before they occur.
Furthermore, we operate our quality management system (QMS) on a process-based approach to ensure processes are efficient. As far as internal audits in particular are concerned, we conducted SPMC Internal Audit Practical Training at three sites to enable the use of SEKISUI CHEMICAL's proprietary assessment tool, the SEKISUI Process Management Chart (SPMC). - 4.Enhancing Communication
We published the STAR 55 Bulletin, which introduces positive examples of CS & Quality. We have also published a booklet called VOICE, which is based on inquiries received from the Customer Consultation Office. In the second half of 2023, we integrated these two tools and launched the inaugural edition of Shining, a new CS & Quality-information magazine. - 5.Providing Thoroughgoing Employee Education
We conduct CS & Quality-related training for new employees every year. We encourage our employees to think about our concept of "CS & Quality management" and what we can do to satisfy our customers, so that they can apply this information in their daily business activities.
CS & Quality Subcommittee
SEKISUI CHEMICAL Group holds twice-yearly meetings of the Sustainability Committee and CS & Quality Subcommittee, which is a subordinate committee, with respect to CS & Quality.
In fiscal 2023, the CS & Quality Subcommittee met twice in total in October and March.
CS & Quality Management Promotion System
- 15-03
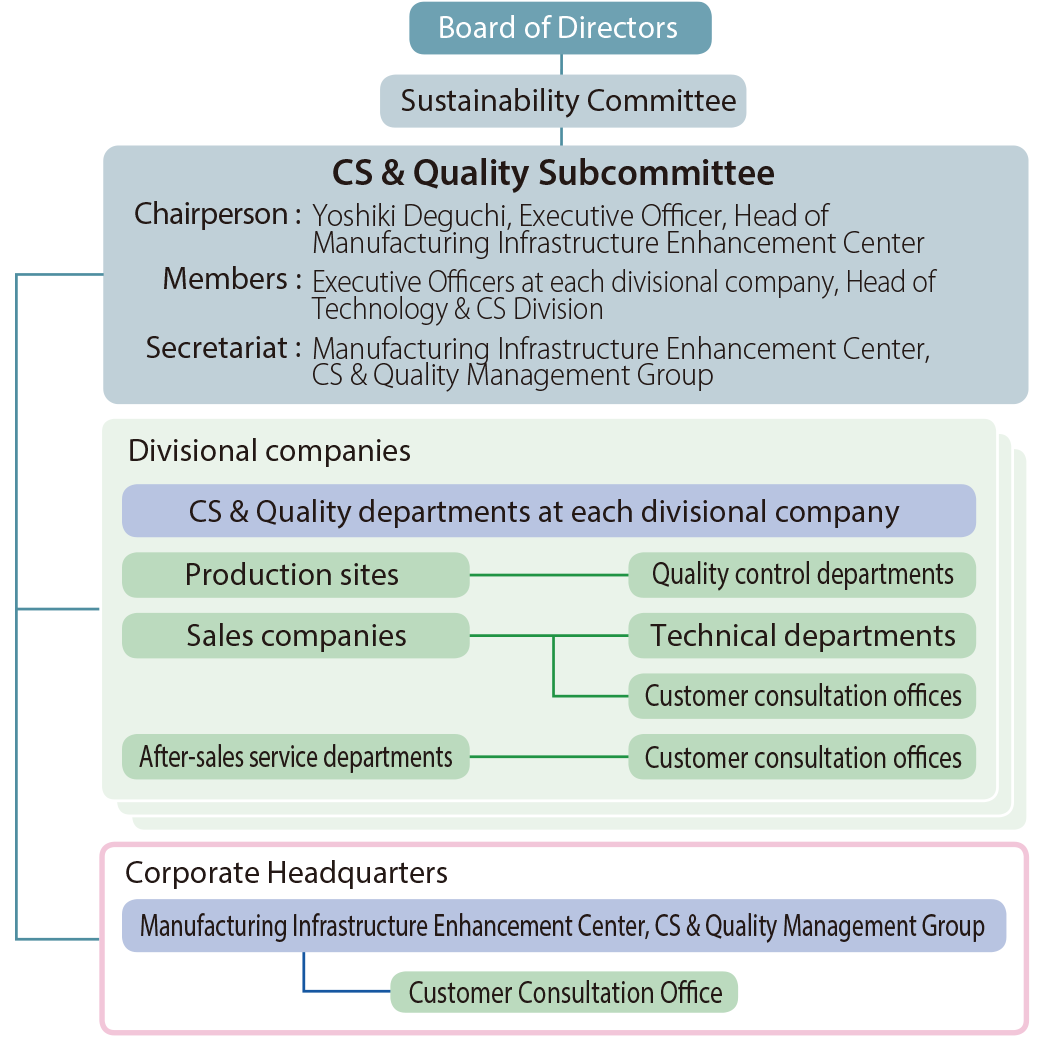
Establishment of a Quality Assurance System
The Group has established a quality assurance system that covers all processes from design and development, production,
and sales.
We have established a quality assurance system for each process and promote daily management with an emphasis
on standards.
At the same time, we are focusing on manufacturing innovation, recognizing that on-site manufacturing is the key
to supporting quality.
In addition, when developing and improving products, we conduct rigorous design reviews from the perspective of quality assurance and safety.
We have also established a system that enables us to sustain and manage services for our customers even after sales are made.
Quality Assurance System
- 09-39
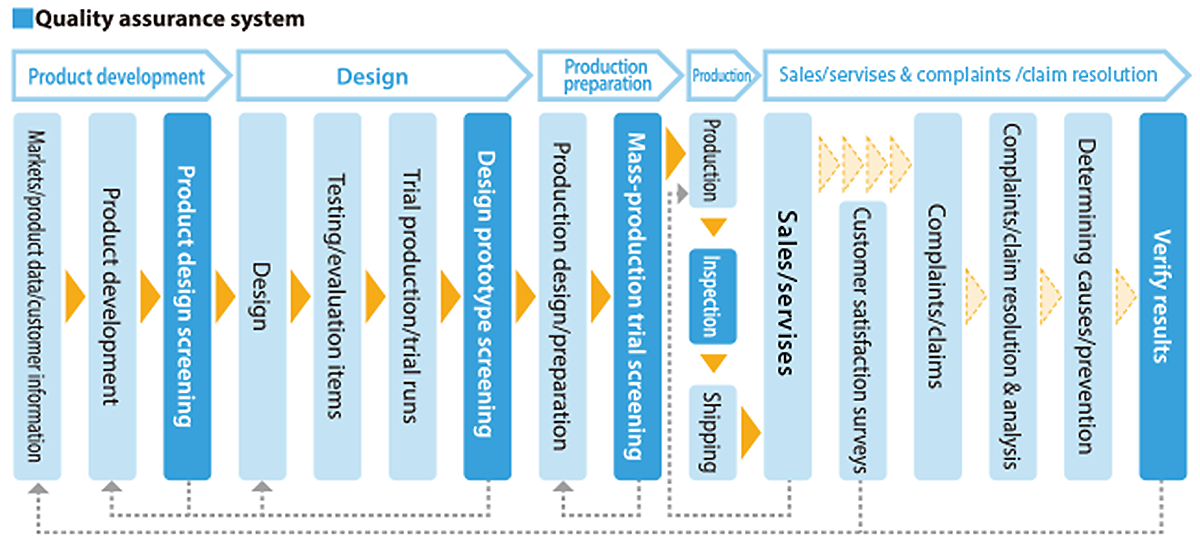
Addressing New Products and Business Risks
SEKISUI CHEMICAL Group considers the occurrence of defects when launching new businesses to be a risk. In order
to reduce this risk, we have established and are operating the Gate Review (GR)* system as a mechanism to conduct
rigorous design reviews.
We use a design check sheet that shows points to be aware of during design, and clarify the points to be discussed during the design review. We also conduct an external knowledge review, which aims to obtain new knowledge from internal and external experts as initial input information for the design of industry, laws, and other matters related to new businesses.
- GR: Systematic activities (checkpoint control function) to determine whether or not to move on to the next stage.
Addressing Existing Business Risks
In promoting its existing businesses, the Group considers major quality issues* to be the risk of solving them first. In order to reduce this risk, we are responding to major quality issues based on a problem-solving flow established to resolve them quickly and appropriately. The executive officer in charge of quality monitors the status of correction of major quality issues that have arisen.
- Major quality issues are issues that will cause serious damage to customers, social, and the Group if we do not urgently resolve the fundamental issues related to the quality of our products, technologies, and services.
Targets
Under the current Medium-term Management Plan, SEKISUI CHEMICAL Group has promoted CS & Quality activities and set "the number of events to improve the level of CS & Quality*" as a KPI in order to prevent damage to the Group’s corporate value due to serious incidents.
The results of the major implementation measures are as follows.
Major Implementation Measures | Management Indicators | Final Fiscal Year (FY2025) Targets of the Current Medium-term Management Plan | FY2023 Results |
---|---|---|---|
Preventing the Occurrence of Serious Quality-related Problems | Implementation of CS & Quality level improvement events | 4 times / year | Conducted three3 CS & Quality seminars and one Group KAIZEN meeting |
- Events to increase the level of CS & Quality: Group-wide CS or Quality improvement events organized by the CS & Quality Group.
Strengthening QMS
Strengthening daily management
When SEKISUI CHEMICAL Group transitioned toward ISO9001:2015 certification, we devised an original management sheet, which we dubbed the SEKISUI Process Management Chart (SPMC), to strengthen our response to process approaches. Illustrating the management flow at a glance, the SPMC can be effectively used for daily management checks, corrective action, internal audits, and other activities, including quality education.
In fiscal 2023, as in fiscal 2022, we held training for QMS internal auditors as well as SPMC Internal Audit Hands-on Training. We also worked to increase the competence of employees by expanding and making use of such tools as the "Voice Video of Internal Audit Scenarios" and “Audit Trail,” an e-Learning course for enhancing the groundwork of internal audits.
We will continue to promote initiatives to improve the quality of our quality management system.
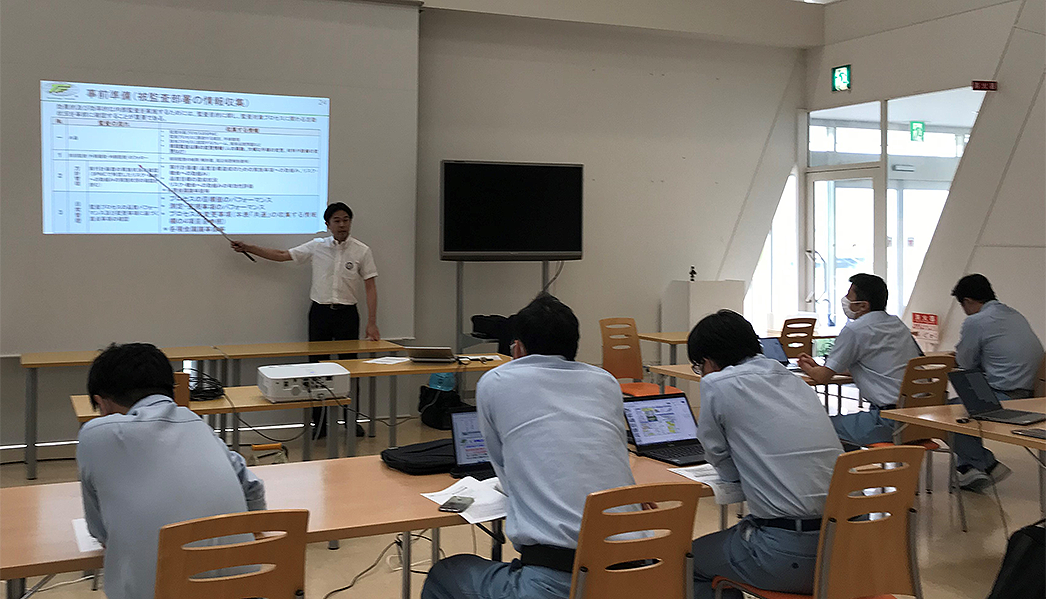
SPMC Internal Audit Hands-on Training
Reinforcing testing data reliability Promoting Efforts to Enhance the Robustness of Inspection Data
Based on the CS & Quality Medium-term Plan launched in fiscal 2020, SEKISUI CHEMICAL Group continues to create and operate systems as well as mechanisms to thoroughly prevent data falsification and manipulation.
In fiscal 2023, steps were taken to confirm the operating status of the system established in fiscal 2022 to prevent data entry errors and manipulation., We also worked to improve the reliability of inspection data and transcripts.
In the future, we will focus on utilizing digitized inspection data to improve the quality of operations.
SEKISUI CHEMICAL Group will continue to strengthen internal quality control and provide quality compliance training to ensure that the Group reinforces its awareness toward compliance. Through these means, we will enhance our quality assurance capabilities and extinguishing any potential for fraud.
Compliance with laws and voluntary regulations regarding product safety
SEKISUI CHEMICAL Group regards product safety as the most important factor in quality. In order to deliver safe products to customers, we strive to ensure the safety of the products manufactured and sold by each Group company.
Safety reviews are conducted at the design and development stage to ensure product safety. In addition, in the event that a legal or regulatory violation related to product safety is confirmed internally or pointed out externally, information is promptly disclosed to the public and steps taken to quickly investigate the cause and prevent a recurrence.
The same applies to violations of product safety standards voluntarily established by Group companies.
In fiscal 2023, there were no cases of violation of various laws and voluntary regulations regarding product safety.
Product quality disclosure and labeling
SEKISUI CHEMICAL Group ensures that all relevant laws and regulations as well as internal rules are strictly observed with respect to the disclosure of information related to product quality and safety.
At the development stage, we set and check items for compliance with laws and regulations relating to product information disclosure, and implement design reviews (DRs).
In fiscal 2023, there were no violations of information disclosure relating to product quality and safety.
Strengthening CS
CS Monitoring
Based on the current Medium-term Management Plan, we launched a CS monitoring program (internal survey) for the purpose of ascertaining and strengthening the ability of Group employees to respond to customers.
In fiscal 2023, when the program was first launched, 7,936 employees responded. In the future, we will reflect the results of each survey in measures to strengthen our ability to respond to customers.
CS & Quality information dissemination
CS & Quality Seminar
The CS & Quality seminar is an in-house lecture held by external experts on a wide range of topics, including case studies of customer satisfaction and the development of organizations/human resources that can provide customer satisfaction. We have held these meetings since fiscal 2001 to raise awareness of CS & Quality. As of the end of fiscal 2022, a total of 64 such meetings have been held.
In fiscal 2023, seminars were held three times: once in the first half and twice in the second half.
-
<The 65th>
Why do incidents of data
falsification continue to occur
TECHNOFA CORP
Chairperson Yoshihito Hirabayashi
(July 24, 2023) -
<The 66th>
Customer feedback is a tool utilized to visualize customers satisfaction.
-Creating a bridge for CS improvement-
Skymark Airlines Inc. Kentaro Toda,
General Manager of CS Promotion Office
Yaryoku Inoue, Assistant General Manager
(December 19, 2023) -
<The 67th>
From Customer Satisfaction (CS)
to Customer Delight (CD)-What is Service Excellence? Graduate School of the University of Tokyo
Associate Professor Tatsunori Hara of the Graduate School of Engineering
(March 21, 2024)
Publication of CS & Quality information tools (STAR 55 Bulletin / VOICE / Shining)
Since 2002, the 55th anniversary of our founding, we have undertaken STAR 55 activities, a Group-wide initiatives
aimed at promoting CS. Since 2004, we have expanded our efforts to engage in CS quality-based management.
As part of these endeavors, we have published the STAR 55 Bulletin, a compilation of positive Group-wide CS &Quality examples since 2006. The 50th issue was published in September 2023.
In addition, in 2015 we launched VOICE, a collection of slightly less than 10,000 customer comments received each year by the Customer Consultation Office and the Group’s subsequent response, with the aim of fostering a CS & Quality culture and encouraging employees to look beyond the business for which they are responsible. The most
recent 8th issue of VOICE was published in July 2023. In 2019, we launched VOICE+ as an additional Web edition
issue, and by March 2024 had published a combined total of 11 VOICE and VOICE+ issues.
In the second half of 2023, we integrated the two tools, STAR 55 Bulletin and VOICE/VOICE+, and launched the new CS & Quality information magazine, Shining. Based on the history of the STAR 55 Bulletin and VOICE/VOICE+, we aim to further enhance the dissemination of CS & Quality information in order to realize Vision 2030. In November 2023, we published the inaugural issue of Shining.
-
● STAR55 Bulletin No.50
(September 2023) -
●VOICE No.08
(July 2023) -
●Shining No.01
(November 2023)
Improving KAIZEN Activity Groundwork
SEKISUI CHEMICAL Group began Group KAIZEN Activities (small-group improvement activities) in 1966 with the aim of improving the on-site manufacturing capabilities that underpin quality. In this manner, the Group is continuing to make improvements after improvements.
Improving the Quality of KAIZEN Activities
The Group provides improvement theme support not only to sites in Japan but also those overseas. As a result, we were able to bolster groundwork and improve the mindsets of support business sites.
Expanding the Scope of KAIZEN Activities
We are implementing a plan to expand the scope of Group KAIZEN Activities to include not only manufacturing but also indirect operations. In fiscal 2023, we held KAIZEN exchange sessions focusing on indirect operations. As a result, we were able to achieve a synergistic effect, with participants saying that they would like to adopt this initiative at their own workplaces.
Group KAIZEN Activity Presentations
Group KAIZEN Activity presentations (Group-wide competition) were held on a Group-wide basis in January 2024.
Under the slogan, "Widening the circle of KAIZEN, enhancing the quality of KAIZEN, and accelerating the KAIZEN process", selected presentation sites participated not only from Japan, but also four overseas regions (Europe, the United States, China, and Asia. In fiscal 2023, all presenters gathered together and were able to present their KAIZEN results face-to-face.
In addition, poster sessions were held in conjunction with each presentation.
Successful steps were taken to promote further exchange and mutual improvement by discussing and exchanging information on more in-depth content that could not be conveyed through presentations alone.
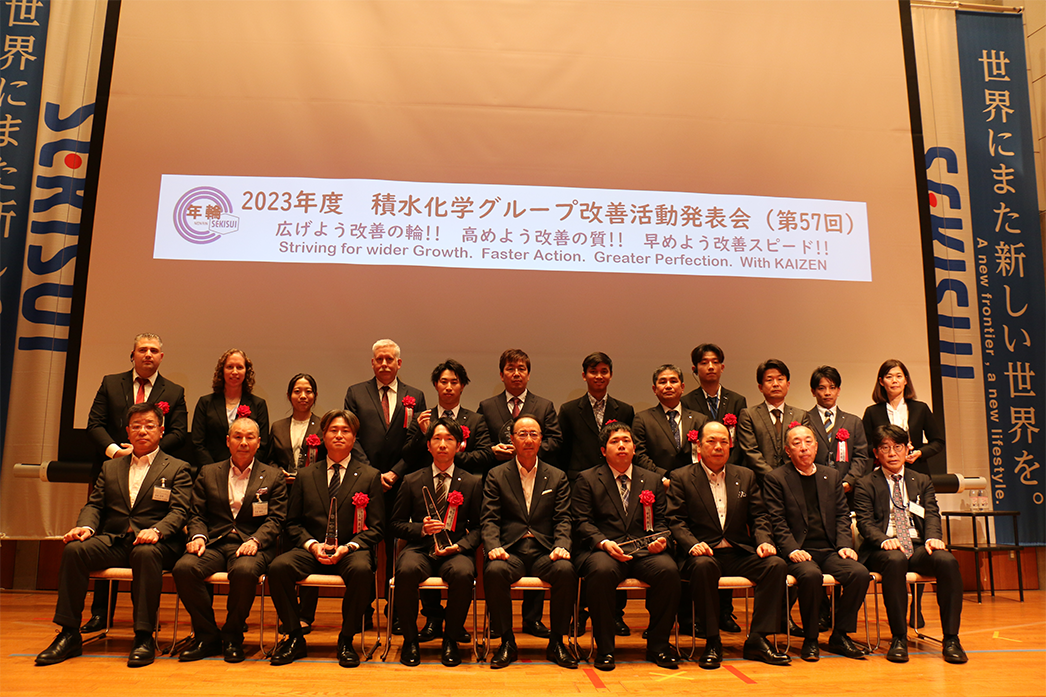
FY2023 Group KAIZEN Presentations
Strengthening CS & Quality Human Resources
SEKISUI CHEMICAL Group conducts a variety of training programs to strengthen its CS & Quality human resources.
We conduct the following training to prevent quality issues.
- Development prevention seminars aimed at teaching effective and efficient prevention methods
- DR*1 Reviewer Training seminars designed to improve the skills of employees engaged in DR
- QFD*2 seminars to impart ways to organize information on new product development
- Guidance and support on GR operations relating to new businesses
In fiscal 2023, we held one development prevention online seminar.
As far as the content of CS is concerned, we conducted training that enables those in charge of each business to acquire and apply methods of designing and analyzing questionnaires in order to strengthen the mechanisms for collecting and utilizing customer feedback.
We are also focusing on digitizing training in an effort to address the shift to teleworking and ensure operational efficiency.
As a result, we have put in place and operate a system that allows anyone to learn on demand at any time.
- DR: Design Review
- QFD: Quality Function Deployment
FY2023 Results
There was one major quality issue in the Group that occurred in FY2023. (Based on individual divisional company
standards)
External loss costs*1 came in at 79% compared with FY2020.
We will continue to strengthen Group-wide quality assurance systems. We will also focus on design/development processes. Moreover, we will promote the use of development preventive measures (such as QFD and DRBFM*2)3 to reduce external loss costs.
In FY2023, the utilization rate of development prevention methods was 100%.
- External loss costs: Costs for handling claims related to products.
- DRBFM: Design Review Based on Failure Mode ( a preventive approach in which problems in new designs are discovered and solved by focusing on points of modification and change)
Data Concerning Major Quality Issues
Number of Major Quality Issues
- 09-78
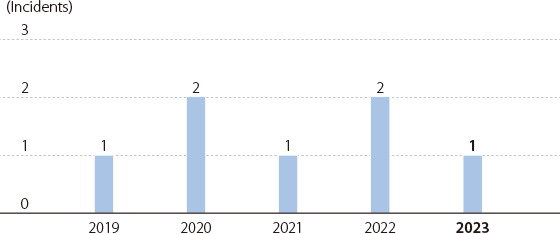
Indicator | Calculation Method |
---|---|
Major Quality Issues | These refer to product and service quality issues determined by Corporate Headquarters
or divisional company presidents, based on evaluations and judgments by the quality
assurance manager, which could cause significant damage to customers, society, or
SEKISUI CHEMICAL Group and lead to the loss of society’s trust in the Group if not
thoroughly resolved on an urgent basis including:
|
Data Concerning External Loss Costs
External Loss Costs
- 09-80
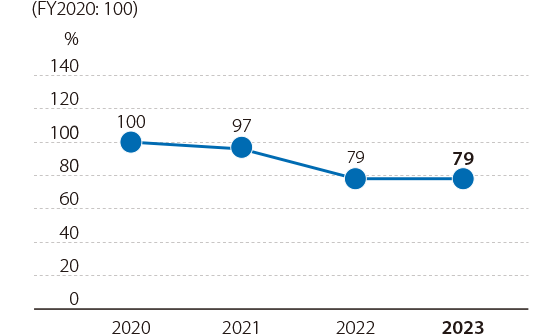
Indicator | Calculation Method |
---|---|
External failure costs |
Costs arising from responding to product-related complaints |
Other Data
Data on incoming calls to the Customer Consultation Office
-
Incoming Contacts Received by the Customer Consultation Office in FY2023
- 15-13
Indicator | Calculation Method |
---|---|
Incoming Contacts Received by the Customer Consultation Office | Number of inquiries by telephone, e-mail, letters, and other means |
-
Breakdown of incoming contacts (SEKISUI CHEMICAL)
- 15-15
Indicator | Calculation Method |
---|---|
Breakdown of incoming contacts |
Incoming contacts are recorded on Insider Net and categorized as follows:
|
Business Sites That Have Received Third-Party Certification for Their Quality Management Systems
Of the total number of SEKISUI CHEMICAL Group's production sites, 88% are ISO 9001 certified, and 99% when ISO 13485 and IATF 16949 are included.