Risk Management
- Strategy(Stance and Approach)
- Governance
- Risk Management and Crisis Management
- Indicators and Targets
- Major Initiatives
(Stance and Approach)
Risk Management Philosophy
In order to realize our Long-term Vision in a rapidly changing business environment, it is essential to take decisive risks and earn the trust, expectations, and peace of mind of stakeholders. SEKISUI CHEMICAL Group believes that risk control and resilience capabilities that enable risk taking are key to this end. Based on this idea, our Group has positioned risk management as one of its management bases and is working to achieve this goal. As our Group engages in risk management, we centrally manage "risk management" and "crisis management" before and after the occurrence of risk events. We believe that this will enable exible risk management without omission, and we have integrated prevention and minimize of the impact when it occurs.
- 09-58
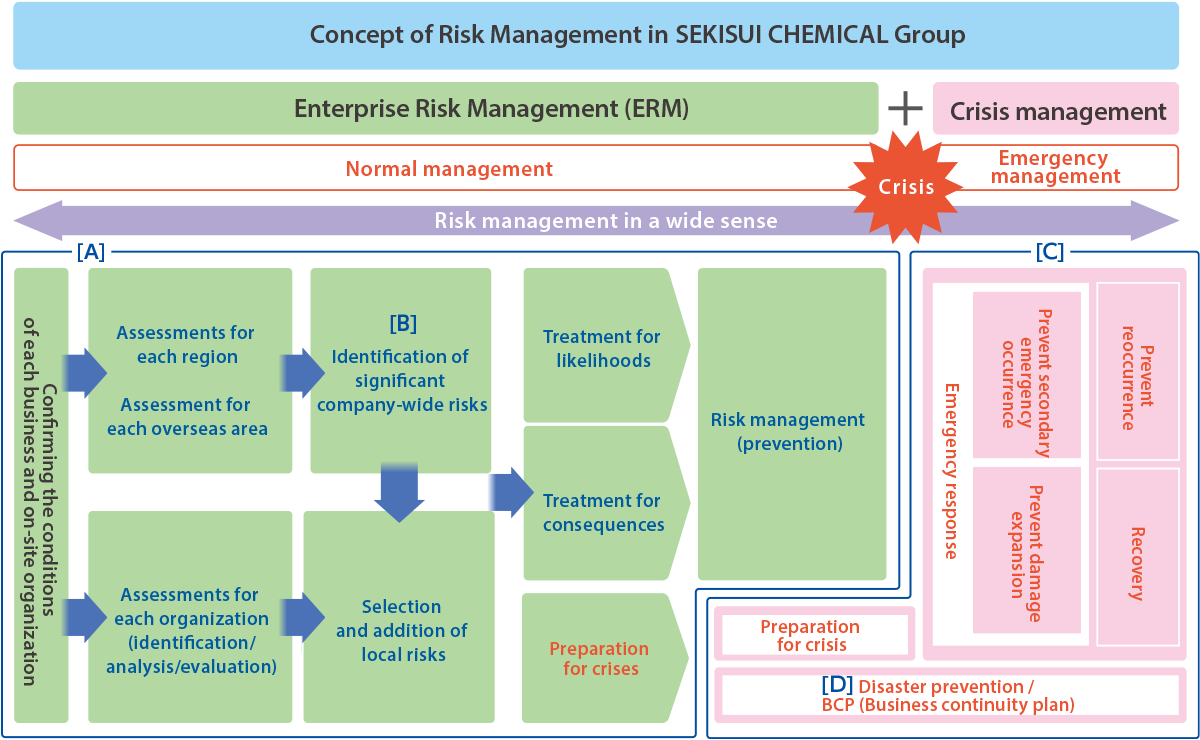
SeeStructure of Risk Management Activities for more information on A and B systems and initiatives; seeEmergency Response Headquarters Functions (when a major earthquake occurs) for more information on C and D initiatives.
Structure of Risk Management Activities
- 05-13
Risk Management System
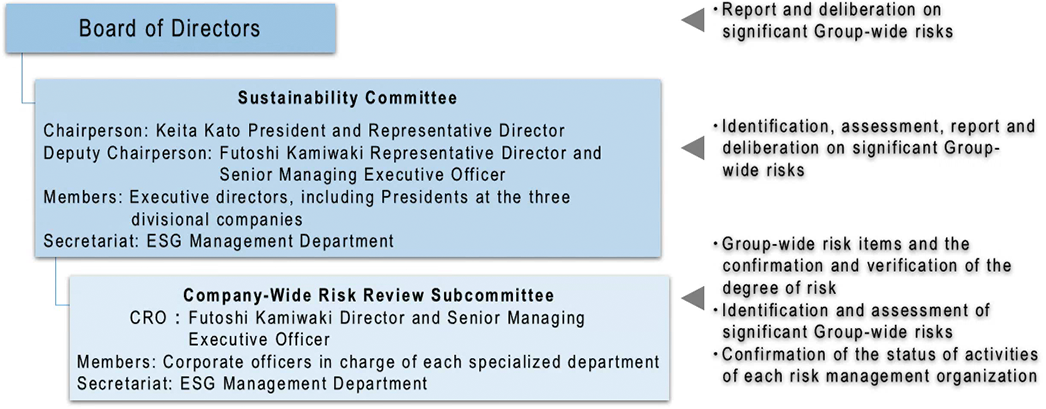
The Group-wide Risk Review Subcommittee, with the participation of the directors in charge of each specialized corporate area, deliberates on whether or not there are any changes in the results and likelihood of correction or correction of major Group-wide risks identified in the previous fiscal year, based on changes in the internal and external environment. The results of deliberations by the Subcommittee and various measures to reduce risks are discussed by the Sustainability Committee and then reported to the Board of Directors. We are also moving forward with initiatives that will be reflected in the risk management activity plans for the following fiscal year in each organization.
ERM (Enterprise Risk Management): A reference to Group-wide risk management.
Amid increasing uncertainty and complexity in the business environment surrounding companies, SEKISUI CHEMICAL Group believes that improving the "risk sensitivity" of its employees is essential for the appropriate management of risks, and continues to implement PDCA cycles in accordance with ISO31000, the international standard for risk management. We comprehensively identify different risks related to the business objectives of each organization, and quantify those risks from the perspectives of "results" and "likelihood of occurrence", etc. In addition, each specialized corporate department identifies "Group-wide major risks" that are likely to lead to serious incidents in the five areas of "safety, quality, accounting, legal and ethical affairs, and information management." By making it mandatory to conduct assessments in organizational risk-management activities, we have built an ERM system to curb serious incidents and share and manage them within the Group. The effectiveness of ERM is continuously verified by regularly checking for uncertainties.
Overseas, starting in fiscal 2023, the Overseas Regional Headquarters identifies risks specific to each region. The operating companies in each region conduct assessments along with "Group-wide major risks" to assess risks specific to each region, and, as in Japan, promote risk management activities in each specialized area.
Increasing Risk-sensitivity Using PDCA Cycles
In the increasingly complex external and internal environment, it is extremely difficult to accurately grasp the risks that may occur in the future. In order to manage risks appropriately, our Group considers it essential to improve the risk sensitivity of its employees, and we continue to implement PDCA cycles that are in line with ISO31000, the international standard for risk management, on an organizational basis. This activity started in fiscal 2011 in 27 organizations, mainly business divisions, and the number of organizations increased year by year. In fiscal 2023, the number of organizations reached 170 domestically and overseas (99% of consolidated sales). Activities in the R & D departments of all in-house companies have also taken root.
- 09-59
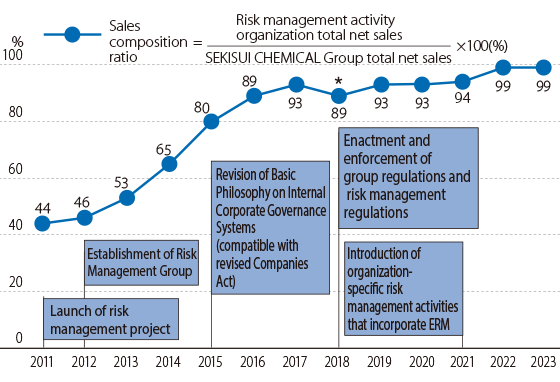
- Temporary decline resulting from a large-scale M&A.
Domestic Crisis Management Organizational Structure
- 09-64
Procedures for contacting divisional companies / Corporate Headquarters from the frontline immediately after an emergency occurs.
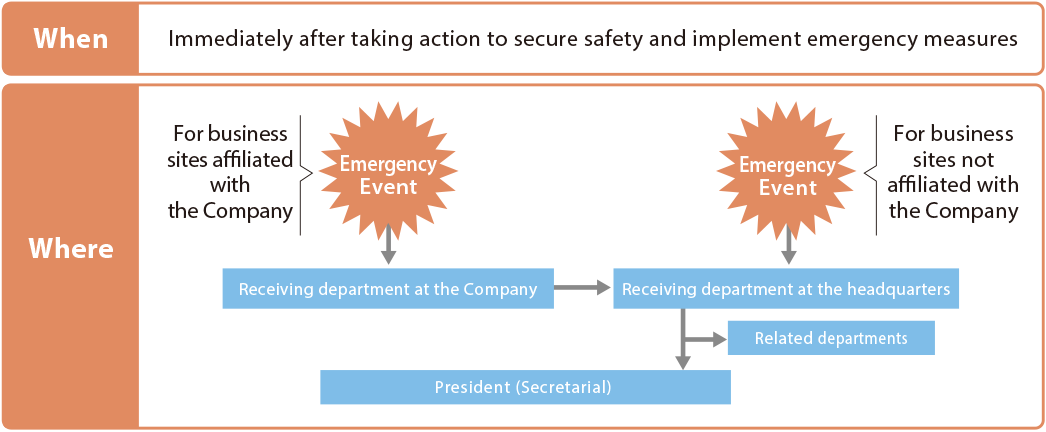
- 09-63
Initial action of the Emergency Response Headquarters (in the event of a major earthquake)
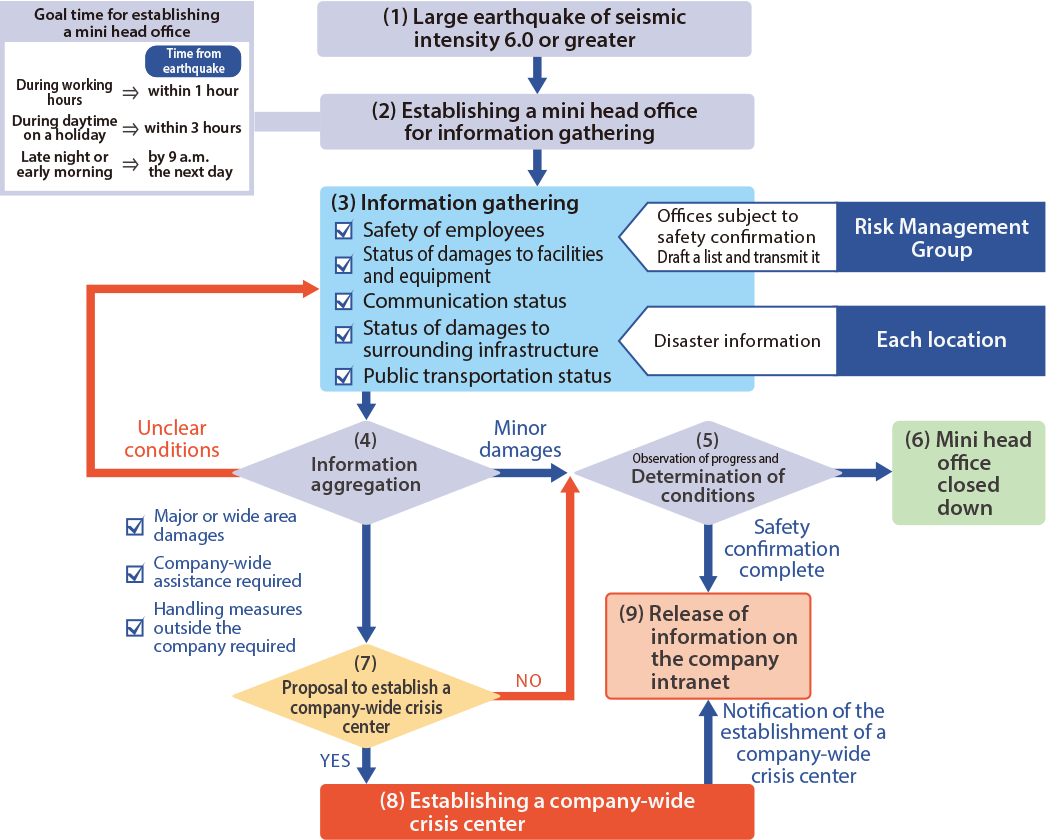
- 09-62
Emergency Response Headquarters Functions (when a major earthquake occurs)
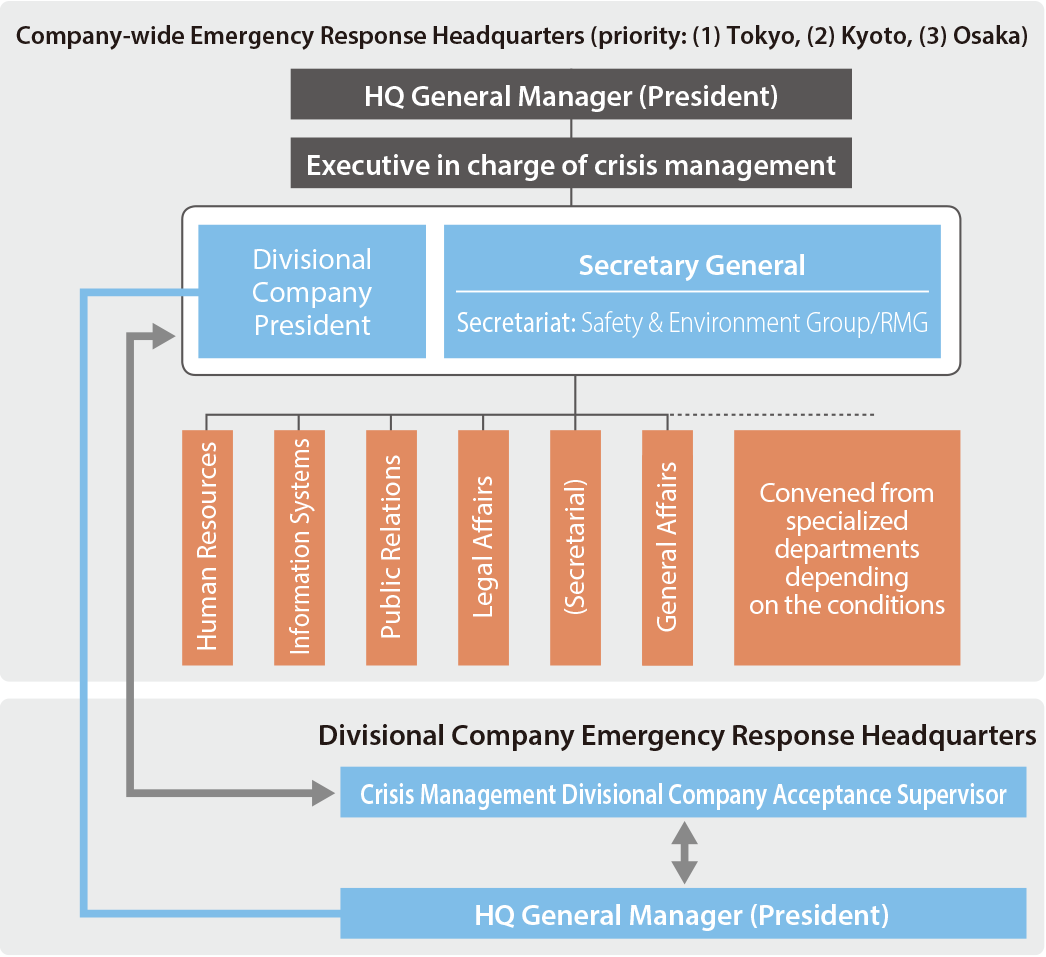
Overseas Crisis Management Organizational Structure
- 05-14
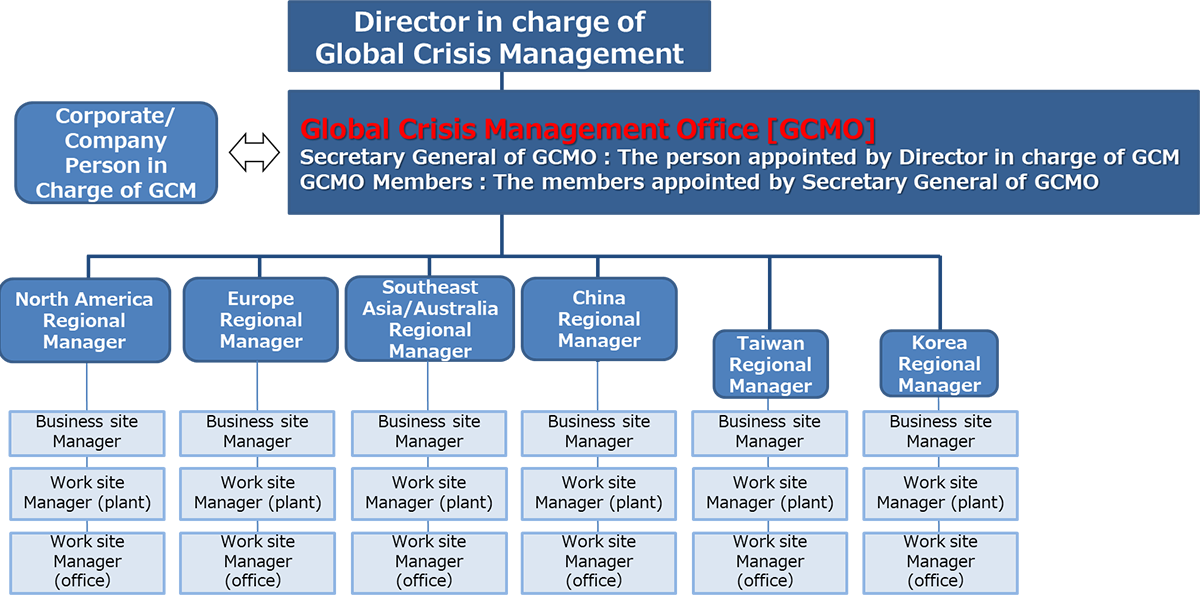
Risk Management
In the past, SEKISUI CHEMICAL Group's risk management focused on identifying and responding to risks in each business and organization (bottom-up approach) in line with the characteristics of a diverse range of businesses and business formats.
In addition to this, the current Medium-term Management Plan identifies risks that could disturb the management of the entire Group (Group-wide major risks) and has built and strengthened a top-down approach system to deploy them in Group-wide measures and in each business and organization.
In the next medium-term plan, we will strengthen our ability to detect risks globally and strengthen our ability to reduce risks by integrating each business and organization with specialized headquarters departments.
Crisis Management
In the wake of the outbreak of COVID-19 as of the end of fiscal 2019, Corporate Headquarters took the lead in developing and renewing BCPs for all organizations while putting in place a BCM system under the current Medium- term Management Plan.
Under the next Medium-term Management Plan, we will work to establish autonomous training programs while conducting reviews for each organization and constantly raising performance.
Targets
Under the current Medium-term Management Plan, SEKISUI CHEMICAL Group has worked to minimize the impact of earthquakes, pandemics, and other incidents by formulating a BCP and achieving a 100% operating rate. In the previous fiscal year, the Group achieved a 100% BCP operating rate. In fiscal 2023, steps were taken to complete the BCM cycle (voluntary training and document revision) and to make the BCP more functional from a practical standpoint.
In our risk management activities, we promoted the overseas deployment of a risk management system (digital dashboard) and completed the introduction of this system to all organizations, thereby creating a system that enables monitoring from domestic business companies, dedicated offices in Corporate Headquarters, divisional company business divisions, and overseas RHQ.
Training Systems
As far as risk management activities by organization is concerned, SEKISUI CHEMICAL Group has conducted training for newly appointed risk managers on an annual basis since fiscal 2017 to ensure the competence of risk managers assigned to each organization. In fiscal 2023, three managers from new and other organizations received training, bringing the total number of participants to 268.
Note: Risk managers: Persons responsible for duties related to risk management activities in their respective organizations
Crisis Management Activities
Based on the experience of the Great East Japan Earthquake, SEKISUI CHEMICAL Group totally reviewed its crisis management system in fiscal 2011. Since then, we have been strengthening the system and mechanisms. Crisis management activities are conducted in accordance with the SEKISUI CHEMICAL Group Crisis Management Guidelines. Crisis management liaison meetings, which are attended by representatives from each Corporate Headquarters group and divisional companies, are held regularly to review case studies and conduct training.
Specifically, we conduct a review of the Emergency Situation Initial Response Procedures Manual through drills attended by members of initial response headquarters across the Group and confirm coordination.
We also distribute the Emergency Situation Initial Response Procedures Manual to all employees every year. This ensures that each individual can make an appropriate initial response in the event of an emergency. In addition, since fiscal 2019, we have installed a safety confirmation system on all employees' mobile phones and other devices so that we can quickly confirm the safety of employees in the event of an emergency.
To combat infectious diseases, we established an infectious disease emergency task force in March 2020 and set up a special page on our intranet for dealing with infectious diseases and disseminating action guidelines and sharing measures to prevent the spread of infectious diseases. In the event that an infected person is identified within the Group, we promptly assess the situation and share information with the people concerned, placing the highest priority on the safety of employees. As a result of these efforts, there was no major impact on our business up until the task force was dissolved in September 2022.
Business Continuity Plan (BCP) Implementation
We have positioned the BCP as an essential tool to support our business strategy. In light of the Group’s divisional company system and wide-ranging business operations, our basic stance is that those in charge of each line of business (the heads of business units, the presidents of business companies, etc.) individually determine the necessity of a BCP according to the nature of the business. Based on this, we have recommended the formulation of a BCP and the implementation of business continuity management (BCM) in line with ISO 22301, which standardizes the method of undertaking BCM. However, as different threats are increasing, it is increasingly necessary to determine how to continue operations in the event of the loss of major management resources over the medium to long term, and to prepare for such loss. Accordingly, all organizations formulated or revised an initial response plan (ERP) with "protecting human life" as the first priority as a Group-wide initiative in fiscal 2021. Major business organizations also developed a resource-based all-hazard BCP to respond to all crisis events.
In fiscal 2022, we made desktop training mandatory for all relevant organizations, verified the effectiveness of and made revisions to ERP documents, and completed a PDCA assessment of the BCM cycle. In addition, with the participation of the presidents of each divisional company, we conducted a task force joint drill to improve the resilience of each divisional company. In fiscal 2023, individual organizations implemented BCM operations autonomously using a simple training tool. In the future, each divisional company will take the lead in developing a system for collaboration among bases and strengthening regional cooperation.
Through the above, in the event of an emergency that could threaten the continuance of operations, we will be able to respond quickly and resume important operations as soon as possible. We are building a system to minimize losses to our organization and customers and to fulfill our social responsibilities as a company.
Emergency Situation Initial Response Procedures Manual (April 2024 revised edition)
-
Japanese edition
-
English edition
Overseas Crisis Management Activities
The Group engages in crisis management across six regions around the world in accordance with its Overseas Safety Management Regulations. The Overseas Crisis Management Office (Risk Management Group, ESG Management Department) plays a central role in sharing risk management information with employees traveling on business, expatriates, and local employees, providing them with timely warnings and instructions on travel restrictions, and taking other measures in normal times and in emergencies. In light of the increasing number of overseas bases and the growing importance of overseas operations, we have established regional headquarters in four major regions and appointed a responsible manager each. In the event of a crisis, the Regional Head and Overseas Crisis Management Office work together to gather information and take initial action. In addition, we are building a more specialized support system in cooperation with security and medical assistance partner companies. We also provide pre-assignment education for employees posted overseas, pre-business trip e-learning for employees on business trips, and country-specific training focused on infectious diseases to educate employees on basic risk-management issues and specific safety measures.
- 09-66
- 09-67
- 09-68
- 09-69
Global Crisis Management Guidelines
-
Japanese edition
-
English edition
-
Chinese edition
-
Korean edition