Safety Issues
- Strategy (Stance, Approach, and Awareness of Risk)
- Governance
- Risk Management
- Indicators and Targets
- Major Initiatives
- Performance Data
(Stance, Approach, and Awareness of Risk)
Basic Concept
Under the current Medium-term Management Plan, SEKISUI CHEMICAL Group has continued to promote safety management activities centered on rebuilding audit systems, clarifying global equipment design standards, improving site qualities, and actively utilizing digital technology.
As a result of these activities, we have firmly instilled activities that help improve the intrinsic equipment safety issues identified in domestic production site safety audits within the following fiscal year. In addition, the number of workplace accidents (in particular, incidents that involve personnel falling off equipment and falling over) decreased due to the activities of key safety personnel at domestic construction sites. There were no major equipment-related accidents (fires or explosions) in Japan or overseas.
In contrast, the following issues were uncovered.
・ Identification of risks associated with equipment-related workplace injuries at production sites and a review of the method and scope of such risks
・ Development of automated detection technologies based on monitoring cameras for the purpose of reducing activities that deviate from rules at construction sites
・ Measures against heatstroke amid the increasingly severe hot summer environment
・ Efforts to ensure intrinsic equipment safety at overseas sites and the development of human resources to promote safety
Risk Awareness
SEKISUI CHEMICAL Group recognizes the following safety-related risks.
-
1.
Serious equipment accidents (fires / explosions)
Injury to the body or damage to the property of employees and neighboring residents, long-term suspension of operations, suspension of customer production, inability to continue business
-
2.
Work-related fatal or serious accidents
Difficulty in securing human resources due to loss of trust and harmful rumors
-
3.
Large-scale leakage of hazardous substances and environmental pollution
Injury to the bodies or damage to the property of employees and neighboring residents, long-term suspension of operations, suspension of customer transactions, incidence of decontamination costs
-
4.
Serious violations of environment-related laws
Business continuity risk due to loss of trust, long-term suspension of operations, suspension of customer transactions, and tightening of regulations
Developing Human Resources Capable of Identifying Dangerous Situations
SEKISUI CHEMICAL Group believes that creating a workplace in which employees can work safely and with peace of mind is a key corporate responsibility and one of management’s most important priorities. Based on this concept, we engage in total safety activities (zero occupational injuries, zero equipment-related accidents, zero commuting-related accidents, and zero extended sick leave) based on the five themes (1) to (5) listed below. However, no matter how safe and secure an environment is, accidents cannot be prevented if each and every employee working there does not take the necessary care. Safety is not possible without the safety endeavors of each individual. For this reason, in addition to safety education and efforts to increase sensitivity to danger, we are also focusing on creating a culture of observing and complying with established rules.
-
(1)Safety management using OHSMS
-
(2)Intrinsic equipment safety*
-
(3)Safety education of employees
-
(4)Risk management, including risk assessment
-
(5)Safety as well as disaster-preparedness audits to evaluate the status of the above activities
- The term for machine safety activities promoted by the Group. These activities promote improvements to unsafe areas of production equipment through intrinsic safety design policies and safeguards.
- Out_S14
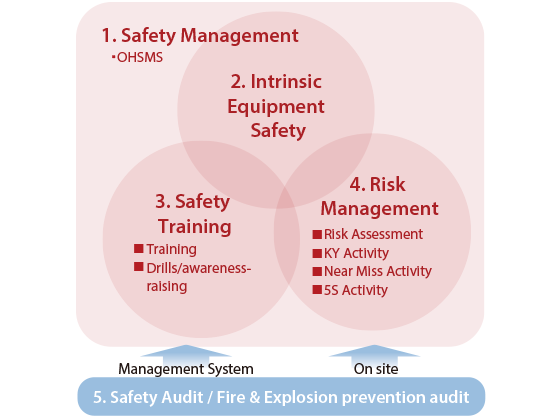
System for Occupational Safety
We have established the SEKISUI CHEMICAL Group Safety Policy as our basic philosophy on occupational safety and share it with all employees.
The Safety Subcommittee, established under the Sustainability Committee, formulates policies and activity guidelines for initiatives related to occupational safety and health. Each site puts into practice and promotes these initiatives under the guidance of the Safety & Environment Group at the Manufacturing Infrastructure Enhancement Center.
We have compiled a wide range of Group occupational health and safety data. This compilation includes data generated from work at production and construction sites and through research activities, as well as from partner companies outside the Group.
The Safety Subcommittee met twice in fiscal 2023, in October and March.
In the event of an actual occupational accident, information, including the employment status of the affected person, is collected. If there are any issues with management at a business site, steps are taken to secure the necessary improvements.
At SEKISUI CHEMICAL Group, the decision on whether or not to acquire ISO 45001 certification is determined on an individual business site basis. The Group then promotes activities to acquire the necessary certification. Sites that have not acquired certification also build and operate safety and health management systems that reflect ISO and OHSAS requirements. We monitor the status of activities through safety and disaster-preparedness audits, and promote efforts to maintain and revitalize safety management activities.
The percentage of ISO 45001 certified business sites (21) to the total number of the Group’s domestic and overseas production sites (91) is 23%.
Business sites (in Japan) that have acquired external certification (ISO 45001)
- SEKISUI CHEMICAL CO., LTD. Shiga-Ritto Plant
- SEKISUI CHEMICAL CO., LTD. Shiga-Minakuchi Plant
- SEKISUI CHEMICAL CO., LTD. Taga Plant
- CHIBA SEKISUI INDUSTRY CO., LTD.
- SHIKOKU SEKISUI CO., LTD.
- TOKUYAMA SEKISUI CO., LTD.
- Sekisui Medical Co., Ltd. Iwate Plant
- Sekisui Medical Co., Ltd. Tsukuba Plant
The percentage of ISO 45001 certified business sites (8) to the total number of the Group’s domestic production sites (46) is 17%.
Business sites (overseas) that have acquired external certification (ISO 45001)
- SEKISUI S-LEC MEXICO S.A. de C.V.
- SEKISUI S-LEC B.V.
- SEKISUI POLYMATECH EUROPE B.V.
- SEKISUI SPECIALTY CHEMICALS EUROPE S.L.
- SEKISUI DIAGNOSTICS (UK) LIMITED
- SEKISUI SPECIALTY CHEMICALS (THAILAND) CO., LTD.
- S AND L SPECIALTY POLYMERS CO., LTD.
- SEKISUI RIB LOC AUSTRALIA PTY. LTD.
- SEKISUI PILON PTY. LTD.
- SEKISUI S-LEC (THAILAND) CO., LTD.
- SEKISUI DLJM MOLDING PRIVATE LTD. Greater Noida
- SEKISUI DLJM MOLDING PRIVATE LTD. Tapukara
- SEKISUI DLJM MOLDING PRIVATE LTD. Chennai 1
- SEKISUI DLJM MOLDING PRIVATE LTD. Gujrat
- Sekisui S-Lec (Suzhou) Co., Ltd.
The percentage of ISO 45001 certified business sites (15) to the total number of Group overseas production sites (45) is 33%
- Out_S15
Safety-promotion System
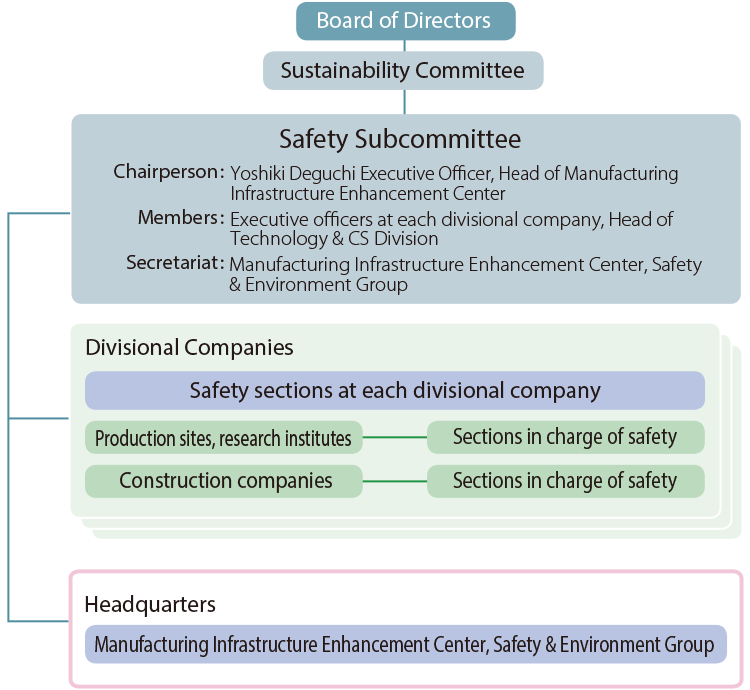
Occupational Safety Committee Meeting Held
SEKISUI CHEMICAL Group holds legally mandated Occupational Safety Committee meetings at each business site. During Occupational Safety Committee meetings, labor and management work together to conduct disaster-related investigations. Strategic proposals related to occupational health and safety are also made.
Meetings of the Central Occupational Safety Committee were held at the Company’s head office up to fiscal 2019. This Committee served as a Group-wide forum for discussion between labor and management. Despite refraining from face-to-face meetings and the hiatus attributable to such factors as the COVID-19 pandemic, deliberations in the form of Central Occupational Safety Committee meetings, at which labor and management discuss issues and measures regarding safety activities, resumed from fiscal 2022.
Declaration of the Commitment to Safe Business Practices Announced by the Leadership of Each Division
SEKISUI CHEMICAL Group recognizes that the most important aspect of safety activities is for the top management of each business site to demonstrate leadership and take the initiative. Based on this understanding, the president and leadership of each division declare their commitment to safe business practices each fiscal year and their personally written declarations are posted on the intranet.
- Out_S16
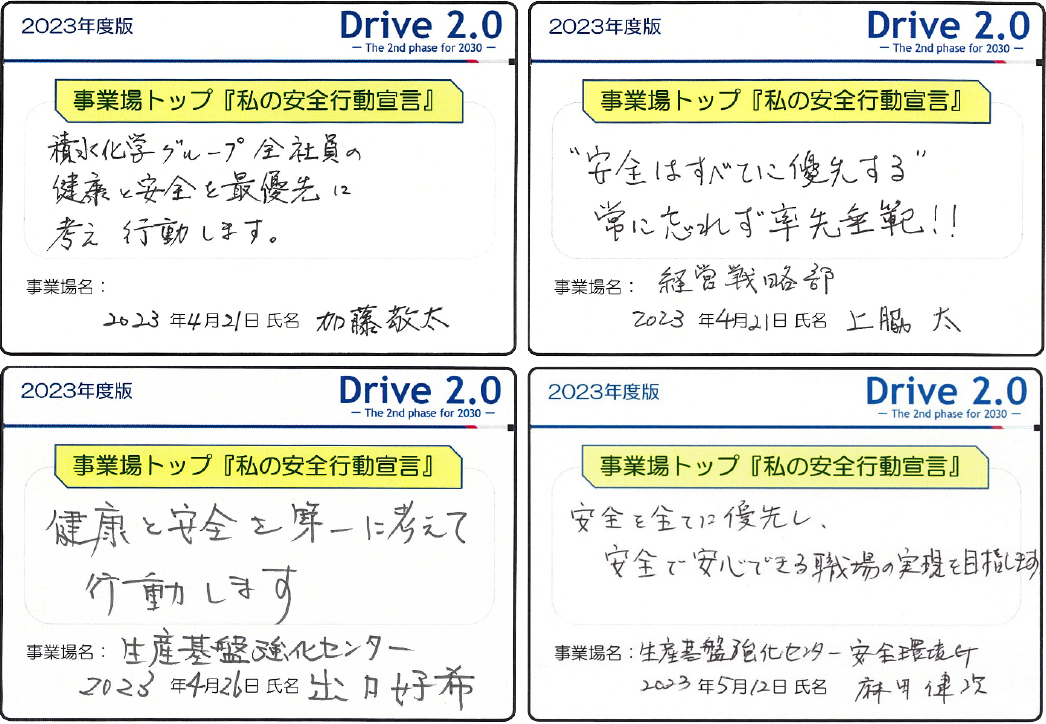
A safety declaration posted on the intranet
SEKISUI CHEMICAL Group identifies and manages safety-related risks as follows.
-
1.
Serious equipment accidents (fires / explosions)
The Group implements risk management by creating equipment management standards to prevent serious equipment accidents, adding equipment assessment items to the management assessment sheet for safety audits, defining equipment management indicators, and utilizing data.
-
2.
Work-related fatal or serious accidents
Injuries caused when caught or entangled in machinery and equipment are highly likely to result in serious permanent disability or fatality. Accordingly, the Group focuses on identifying and mitigating the relevant risks.
-
3.
Large-scale leakage of hazardous substances and environmental pollution
In addition to identifying business activity risks that could have a significant impact on the environment in advance and implementing preventive measures, the Group undertakes activities to prevent large-scale spills outside of business sites through drills that anticipate the occurrence of such risks.
-
4.
Serious violations of environment-related laws
By specifying environment-related laws and regulations applicable to each business site and conducting environmental audits based on these audit standards, the Group engages in activities to prevent serious violations of laws and regulations at business sites.
Implementation of Safety Audits
SEKISUI CHEMICAL Group has identified occupational health and safety management system evaluation categories, which are employed in the self-evaluations conducted at each business site as well as safety audit evaluations by Corporate Headquarters. We review evaluation categories each year, taking into account issues related to Group-wide safety management activities.
In fiscal 2023, safety audits were conducted at 15 domestic sites. This was the first time since fiscal 2019 that all of our business sites had carried out on-site inspections. We were able to conduct document reviews including the close exchange of information, and site inspections from a broader perspective. In the future, the Group plans to make continuous improvements to its safety auditing procedures, to ensure that they are carried out appropriately in line with audit objectives and the circumstances in each case.
Implementation of Occupational Safety Assessments
Article 14 of the Group's Safety Management Rules stipulates that when launching a new business, the general manager of the relevant business division is responsible for conducting a comprehensive prior assessment of occupational safety. Based on this stipulation, the relevant divisional company that is looking to launch a new business implements an assessment.
Laws and regulations at overseas sites differ depending on the region, country, and state. For this reason, external consultants (experts in local laws and regulations) conduct audits to confirm the status of legal compliance.
Implementation of Medical Examinations
SEKISUI CHEMICAL Group provides medical examinations for employees based on the results of medical examinations in accordance with the Employment Evaluation Guidelines for High-risk Employees (for health management officers). In addition, we confirm through safety audits and other means that the following legally mandated health checkups are conducted at each business site.
- Special medical examinations
- Medical examinations for those engaged in designated work
Targets
Under the current Medium-term Management Plan, SEKISUI CHEMICAL Group is promoting safety activities based on the KPI of zero incidents of injuries attributable to machines and equipment with the aim of preventing serious accidents that could result in permanent disability by preventing injuries caused when caught or entangled in machinery and equipment. In FY2023, there were eight incidents of injuries attributable to machines and equipment.
Key Implementation Measures | Management Indicators | Final Fiscal Year (FY2025) Targets of the Current Medium-term Management Plan | Number of incidents in FY2023 |
---|---|---|---|
Safety audits, mutual on-site inspections, comments and sound improvements through on-site risk assessment | Zero incidents of injuries attributable to machines and equipment | 0 | 8 |
Development of Human Resources to Take the Initiative in Safety Activities
To strengthen its safety activities, SEKISUI CHEMICAL Group established and has continued to promote a Safety Leader (SL) certification system since fiscal 2017. Certified SLs assist safety managers and promote safety management activities at each site.
In fiscal 2023, 27 employees (and a cumulative total of 184 since fiscal 2017) were certified under the SL certification system.
SLs are tasked with identifying and mitigating risks at their respective workplaces, holding workshops with other SLs Group-wide, upgrading and expanding the content of safety training, and promoting the rollout of best practice examples.
In addition, since fiscal 2017, we have continued to support employees in their efforts to acquire Safety Sub-assessor (SSA)* certification, holders of which promote machine safety activities. As of March 2024, a cumulative total of 225 employees have qualified with 193 holding certification. Furthermore, 23 employees have acquired Safety Assessor (SA)* certification, while two have acquired Safety Senior Assessor (SEA)* certification, which rank above SSA.
- A safety qualification by Japan Certification Corporation that certifies knowledge of machinery safety based on international safety standards.
New Equipment Design Safety Standards
The New Equipment Design Safety Standards, which summarize the safety specifications necessary for production equipment used by the Group, began undertaking Intrinsic Equipment Safety*1 activities. At the same time, following an update to reflect ISO/JIS machine safety criteria, these Standards now serve as an important document for improving production equipment.
The New Equipment Design Safety Standards have been systematized in accordance with ISO/IEC Guide 51 and are comprised as follows.
-
Standard A:Basic safety standards
-
Standard B:Common safety standards
-
Standard C:Individual equipment safety standards
In 2020, we established the Revision Committee which consists of 12 individuals with SSA*2 qualifications. This Committee updates these Standards with the goal of revising the content once a year.
- Machine safety activities promoted by SEKISUI CHEMICAL Group. These activities promote improvements to unsafe areas of production equipment through intrinsic safety design policies and safeguards.
- A safety qualification by Japan Certification Corporation that certifies knowledge of machinery safety based on international safety standards.
Increasing Opportunities to Uncover Risks and Deploying Best Practices through Mutual On-site Inspections
Since fiscal 2021, the Group has conducted mutual on-site inspections among its manufacturing sites. This initiative is led by the Technology & CS Promotion departments of each divisional company, and involves employees from different manufacturing sites, who work to uncover risks at each other's sites. Previously, safety, accident-prevention, and environmental audits were only conducted once every three years making frequent audits impossible. This made it difficult to horizontally deploy best practice examples of other business sites.
Mutual on-site inspections help improve the awareness of and sensitivity to risks of participating employees, while allowing site leaders and others hosting inspections to learn from other business sites. This has made it easier to reaffirm risks at workplaces and to quickly deploy best practices horizontally.
In addition, the Safety & Environment Group prepares and distributes the Site Risk Identification Handbook as a guideline for uncovering risks on one’s own to safety officers at each business site.
- Out_S17
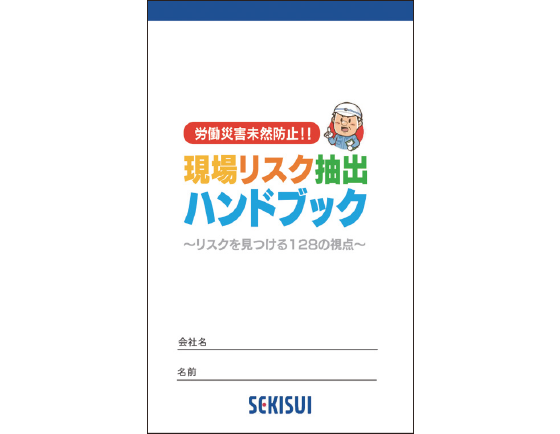
Improving Emergency Response Skills
SEKISUI CHEMICAL Group has identified the following as high risk scenarios that require particular focus with respect to prevention.
- Getting caught or entangled in machinery at production sites
- Falling off equipment or falling over at a business site
- Chemical process-related fires or explosions
Moreover, the Company conducts Heads-up Training where chemical processes are integral to production. At SEKISUI CHEMICAL Group, we conduct Heads-up Training to strengthen the decision-making capabilities of all our employees in the event that they encounter an emergency situation. More specifically, supervisors with years of experience will ask trainees what they would do if equipment designed to prevent danger fails. Trainees are then tasked with providing responses off the top of their heads. This training improves the skills needed to respond to unexpected situations in the event of a disaster by passing down to younger employees the on-site safety know-how accumulated over many years by senior employees. Through this training, we are able to improve equipment countermeasures and revise operating procedures. In addition to teaching trainees how to handle potential problems (troubleshooting), training is applied on various occasions, including evacuation as well as disaster prevention drills.
Deepening Understanding of the Basic Safety Principles
SEKISUI CHEMICAL Group is working to prevent occupational injuries caused by manufacturing machines and equipment through activities that ensure intrinsic equipment safety*. At the same time, we are endeavoring to prevent occupational accidents caused by the actions of workers. Based on the lessons learned from past occupational accidents that have actually occurred at Group sites, we have formulated and are implementing the Basic Safety Principles, which summarize the rules to be observed and prohibited matters during work across six categories for each work process.
In order to ensure that these principles are quickly disseminated throughout the Group, posters with illustrations and easy-to-understand explanations were prepared and distributed to all business sites in Japan and overseas.
- Machine safety activities implemented by SEKISUI CHEMICAL Group. These activities promote improvements to unsafe areas of production equipment through intrinsic safety design policies and safeguards.
- Out_S18
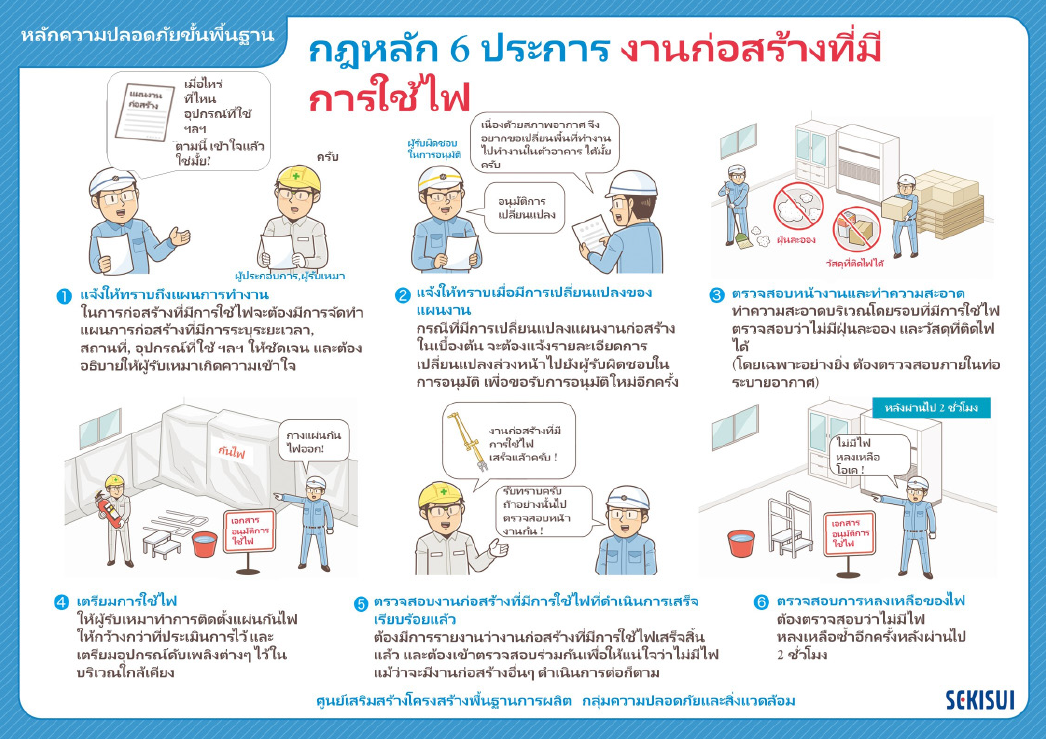
Six Basic Principles for Hot Work Poster (Thai version)
Measures to Prevent Fires and Explosions
Fires and explosions have a significant impact on the surrounding environment and on business continuity. As a preventive measure, we invite outside disaster prevention experts to undertake disaster-preparedness audits when conducting safety audits.
We verify such items as the storage and handling status of hazardous materials as well as the recovery systems used in the event of a natural disaster, etc., to detect disaster risks at an early stage and take preventive measures.
In fiscal 2023, these was audits were conducted at 16 sites uncovering 432 items. As a result, each business site is making the necessary improvements.
- Out_S19
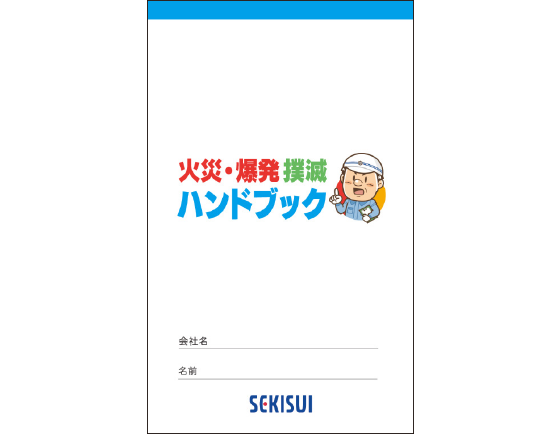
Type of audit | Target / Aim of audit |
---|---|
Safety audit |
|
Disaster-preparedness audit | Primarily consists of audits for accident-prevention measures relating to business continuity
|
Safety Audits at Overseas Business Sites
SEKISUI CHEMICAL Group has established and deployed global safety standards to raise the level of safety activities at overseas production sites, which operate within different legal, regulatory, and cultural environments.
In fiscal 2023, auditors went directly to business sites to conduct on-site inspections. We also conducted an occupational health and safety management audit based on the Group’s evaluation standards through remote meetings for sites that had completed on-site inspections.
Safety Awards
We hold the SEKISUI CHEMICAL Group Safety Conference every year.
In fiscal 2023, awards were bestowed by the president, and case studies presented by sites with the best safety records using an online format on May 26.
Safety Management Across Supply Chains
The Housing Company has organized the Sekisui Heim Cooperation Association with its partner companies (contractors) to ensure the safety of employees of partner companies (contractors) involved in the on-site construction of houses, and holds regular meetings and other events. At these meetings, the Housing Company shares the Group's safety policy, holds safety education sessions, and provides various training opportunities related to occupational safety.
Emergency-preparedness Drills
Each business site conducts emergency response and notification drills to prevent environmental pollution in the event of an emergency and to prevent the spread of pollution. Training is conducted at least once a year, assuming a variety of cases depending on the characteristics of the site.
Environment-related Complaints and Accidents
Environment-related Complaints and Accidents (FY2023)
Category | Number of cases | Details | |
---|---|---|---|
Accidents | Fires | 1 | A catalytic combustion device caught fire and some of the machine's connections burned. The fire was extinguished by the public fire department without any injuries. |
Leakage | 0 | ー | |
Complaints | 0 | ー |
Indicator | Calculation Method |
---|---|
Fires | Number of fire incidents involving firefighting activities by public fire departments that occurred during the fiscal year |
Leaks | Number of incidents involving the off-site leakage of hazardous or toxic materials of 1/5 or more of the designated quantity or 200 liters or more that occurred during the fiscal year |
Complaints | Number of complaints that could significantly affect the living environment of neighborhood residents that occurred during the fiscal year |
Safety Performance
Japan
Aggregate scope: 48 production sites and 5 research institutes in Japan
- Out_S20
- Out_S21
-
Number of Occupational Accidents
Indicator Calculation Method Number of Occupational Accidents The number of occupational accidents (both those resulting in lost time and those not) occurring during a given fiscal year (April through the following March) -
Number of Facility Accidents
Indicator Calculation Method Number of Facility Accidents The number of incidents where facilities malfunctioned (fires, leaks, etc.) that fulfill at least one of the following criteria (SEKISUI CHEMICAL Group criteria), from (1) to (3), occurring during a given fiscal year (April through the following March) -
(1)Human harm: An accident causing at least 30 days’ lost work
-
(2)Material harm: 10,000,000 yen or greater
-
(3)Opportunity loss: 20,000,000 yen or greater
-
- Out_S22
- Out_S23
-
Number of Cases of Long-term Sick Leave
Indicator Calculation Method Number of Cases of Long-term Sick Leave Describes leave of 30 days or more consecutively for sickness or injury occurring in a Japanese production site or research institute during the given fiscal year (April to the following March), and which is newly-occurring. Recurrences within 6 months of the start of work attendance are not counted. However, leave attributable to an occupational injury is counted as an occupational accident and not classified as long-term sick leave -
Number of Commuting Accidents
Indicator Calculation Method Number of Commuting Accidents The number of accidents occurring during commutes to Japanese production sites and research institutes during a given fiscal year (April to the following March); counting assault, damage, self-inflicted injury, and accidents; includes accidents while walking
- Out_S24
- Out_S25
-
Frequency Rate Over Time
- Source of information for the Japanese manufacturing industry: Ministry of Health, Labour and Welfare, Survey on Occupational Accidents
Indicator Calculation Method Frequency Rate The total number of injuries, illness and fatalities in occupational accidents with lost time per 1,000,000 hours of total time worked during a given fiscal year (April through the following March)
Formula for calculation: (Number of injuries, illness and fatalities in occupational accidents with lost time /
total number of man-hours worked) × 1,000,000 -
Severity Rate Over Time
- Source of information for the Japanese manufacturing industry: Ministry of Health, Labour and Welfare, Survey on Occupational Accidents
Indicator Calculation Method Severity Rate The total number of days of work lost per 1,000 hours of total time worked during a given fiscal year (April through the following March)
Formula for calculation: (Number of days of work lost / total number of man-hours worked) × 1,000
- Out_S26
- Out_S27
-
Lost Time Injury Frequency Rate (LTIFR)
Indicator Calculation Method Lost Time Injury Frequency Rate (Number of accidents causing sick leave / total number of man-hours worked) × 1,000,000 -
Occupational Illness Frequency Rate (OIFR)
Indicator Calculation Method Occupational Illness Frequency Rate (Occupational illnesses / total number of man-hours worked) × 1,000,000 Occupational illnesses as defined by the Ministry of Health, Labour and Welfare, including heat stroke, lower back pain, and intoxication by chemical substances
- Out_S28
- Out_S29
-
Safety Performance in the Housing Company’s
Construction SitesIndicator Calculation Method Safety performance on the Housing Company’s construction sites The number of occupational accidents (both those resulting in lost time and those not) occurring on construction sites under the jurisdiction of the Housing Company during a given fiscal year (April through the following March) -
Safety Performance with Respect to Construction Sites in the Urban Infrastructure & Environmental Products Company
Indicator Calculation Method Safety Performance with Respect to Construction Sites in the UIEP Company The number of occupational accidents (both those resulting in lost time and those not) occurring on construction sites under the jurisdiction of the UIEP Company during a given fiscal year (April through the following March)
Overseas
Aggregate scope: 45 overseas production sites
- Out_S30
-
Number of Occupational Accidents
Indicator Calculation Method Occurrence of occupational accidents at overseas production sites and research institutes The number of occupational accidents (both those resulting in lost time and those not) occurring at overseas production sites and research institutes during a given fiscal year (April through the following March)
Japan and Overseas
-
Aggregate scope:48 production sites, 5 research institutes, and 31 construction offices in Japan
45 production sites overseas
Number of fatalities due to occupational accidents
FY2019 | FY2020 | FY2021 | FY2022 | FY2023 | ||
---|---|---|---|---|---|---|
Employees | 0 | 0 | 0 | 0 | 0 | |
Japan | 0 | 0 | 0 | 0 | 0 | |
Overseas | 0 | 0 | 0 | 0 | 0 | |
Partner Companies (contractors) | 0 | 1 | 0 | 0 | 0 | |
Japan | 0 | 1 | 0 | 0 | 0 | |
Overseas | 0 | 0 | 0 | 0 | 0 | |
Total | 0 | 1 | 0 | 0 | 0 |
Health and Safety / Accident Prevention Costs
Aggregate scope: 46 production sites, 5 research institutes, Corporate Headquarters departments, and back offices of divisional companies in Japan
Accident Prevention Costs (FY2023)
Item | SEKISUI CHEMICAL Group | ||
---|---|---|---|
Classication | Details | Expense amount | Investment amount |
1) Costs within business site areas | Health and safety measures, rescue and protective equipment, measurement of work environment, health management, workers’ accident compensation insurance, etc. | 1,307 | 5,192 |
2) Administrative costs | Establishment and implementation of OHSMS, safety education, personnel costs, etc. | 2,223 | - |
3) Other | Safety awards, etc. | 4 | - |
Total | 3,534 | 5,192 |
- Out_S32
- Out_S33
-
Costs and Investments Over Time
Index Calculation Method Costs Costs associated with health and safety as well as accident prevention activities during a given fiscal year (April through the following March) Investment amounts The amount invested in health and safety as well as accident prevention-related measures authorized during a given fiscal year (April through the following March) -
Note:Collated after adding maintenance costs (production, logistics, and power transformer facility management) to costs within business site areas from FY2021.
-
-
Loss Costs Over Time
Index Calculation Method Loss costs The costs of responding to, and the labor costs incurred due to, occupational accidents, facility accidents, commuting accidents, and long-term sick leave due to illness occurring within a given fiscal year (April through the following March)