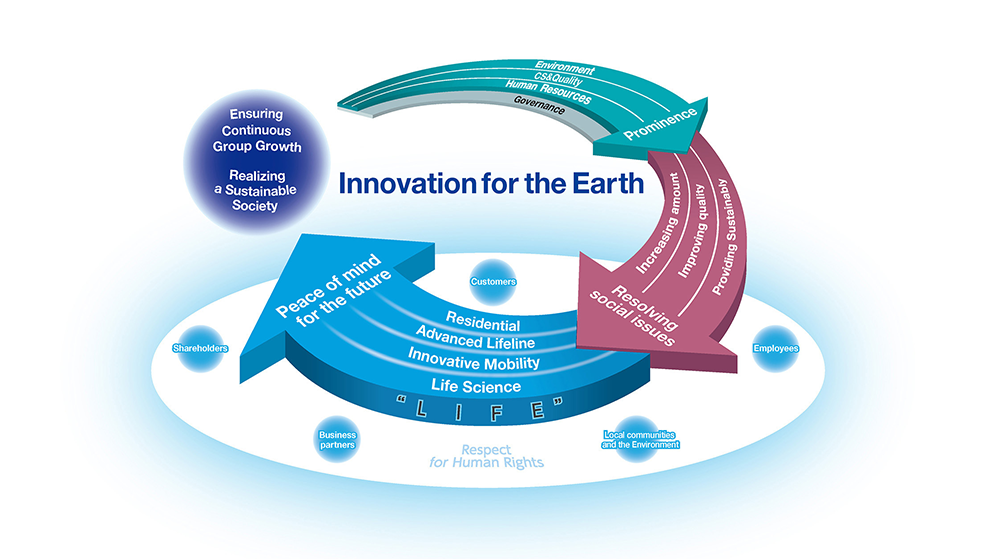
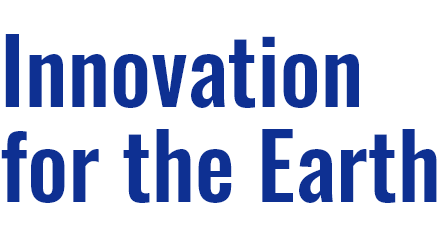
In order to realize sustainable society, we support the basis of LIFE and will continue to create peace of mind for the future.
Updated information
-
- Mar.31, 2025
- SEKISUI CHEMICAL Attains Highest Rank in the DBJ Environmentally Rated Loan Program of the Development Bank of Japan
-
- Feb.13, 2025
- SEKISUI CHEMICAL ranked in Top 10% of S&P Global Sustainability Yearbook 2025
-
- Feb. 7, 2025
- SEKISUI CHEMICAL recognized by CDP with double ‘A’ score for Climate Change and Water Security, and ‘A-’ score for Forests
-
- Dec.24, 2024
- SEKISUI CHEMICAL CO., LTD. has been included in the Dow Jones Sustainability Indices World Index For 13th Consecutive Year
-
- Dec.1, 2024
- SEKISUI CHEMICAL Group's Basic Policy on Customer Harassment
Download PDF
SEKISUI CHEMICAL Group's sustainability data is available in PDF format.