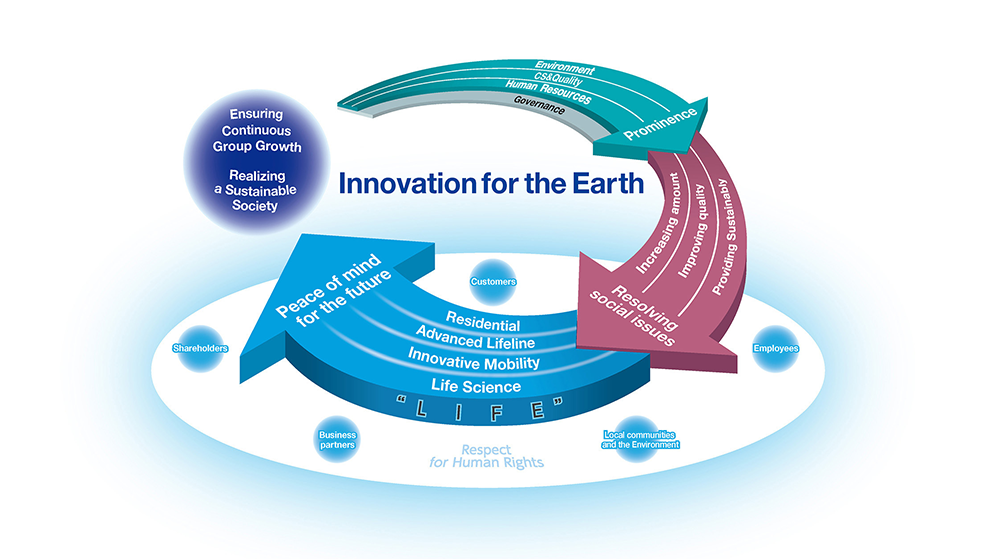
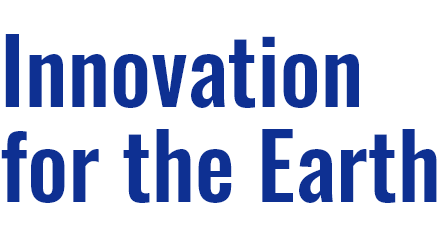
In order to realize sustainable society, we support the basis of LIFE and will continue to create peace of mind for the future.
Updated information
-
- July 9, 2025
- SEKISUI CHEMICAL Receives Highest Rating in the CDP's FY2024 Supplier Engagement Assessment
-
- Mar.31, 2025
- SEKISUI CHEMICAL Attains Highest Rank in the DBJ Environmentally Rated Loan Program of the Development Bank of Japan
-
- Feb.13, 2025
- SEKISUI CHEMICAL ranked in Top 10% of S&P Global Sustainability Yearbook 2025
-
- Feb. 7, 2025
- SEKISUI CHEMICAL recognized by CDP with double ‘A’ score for Climate Change and Water Security, and ‘A-’ score for Forests
-
- Dec.24, 2024
- SEKISUI CHEMICAL CO., LTD. has been included in the Dow Jones Sustainability Indices World Index For 13th Consecutive Year
Download PDF
SEKISUI CHEMICAL Group's sustainability data is available in PDF format.